Club Night Report
Wednesday 11th September 2013An evening with Colin Fullbrook - observations by Vernon Hughes
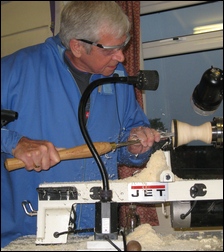
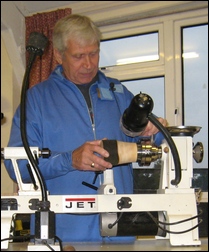
Non-professional woodturner Colin Fullbrook (Vice Chairman of the Gloucester Association of Woodturners) made two natural edge pieces; a vase in freshly cut Sycamore branchwood before the break and a small bowl in dry Laburnum in the second half. But how that brief statement undervalues the occasion! His craft mastery and presentational authority shone throughout the evening.
My aim in this report will be to highlight particular points of value and observations made during the evening rather than to describe his procedures step by step. The methods are, after all, well covered in books, DVDs, videos, etc.
![]() |
![]() |
![]() |
Colin called attention to the light he would be using to determine the wall thickness of the vase and achieve visual maintenance of that dimension as he worked down the piece. He advised careful selection of powerful gripping jaws when working with green wood and stressed the importance of checking that grip from time to time. The welcome lack of dust was also mentioned. Despite the small size of the blank he used a heavy-duty bowl gouge to true the face before drilling a pilot hole down the centre using a tape wrapping on the drill to mark the intended drilling depth. The bowl gouge was used to hollow the vase and both pushing and pulling cuts were employed. Then came that beautiful (did he say 'French Curve'?) round-nosed scraper! At 'unsheathing' its quality and shape had me sitting bolt upright. At the break I leapt forward to get a close look and Colin gave me his full attention in describing it. It had started life as a skew chisel and he had converted it on his grinder achieving the very long, perfectly curved side edge with rounded tip and flawless bevel, freehand but with a carefully set toolrest. Superb work!
He then introduced us to his original design depth gauge (more later) before embarking on his way with wet sanding. He used 'Abranet' in grades between 120 and 320 and showed us his 'cut-outs' for ease of identification - i.e. one notch for 120, two for 180, etc. Each piece of abrasive was immersed in water before use as an aid to clearing dust after use and for airborne dust reduction. Turn down the speed for sanding, he said, to avoid heat generation (particularly important with wet wood subject to distortion/ splitting). For the same reason he valued his light (see above) which importantly produced no heat. The light emitted through the vase wall happened to be an unusual strong pink shade - which easily showed where the wall was thicker in some areas than others. He emphasised the care needed when sanding natural edge pieces which he performed with hand-held abrasive inside and out and using one hand to steady (rigidify) the wrist of the active hand. Interesting! He advised that intact bark edges will stay on and be kept in position by shrinkage. Using oil as a finish will slow the drying process a little; he used (Gilly Stephenson's brand) Australian orange oil. A small foot was turned and the piece was finally parted off to leave a concave base. The finished piece had a very pleasing appearance with its almost black rim sitting above the white Sycamore.
![]() |
![]() |
![]() |
![]() |
His blank of dry timber was approx. 5" in diameter and he had pre-drilled it with a 25 mm Forstner bit to a depth of 50 mm, and had also prepared the spigot for mounting. Once mounted, his first action was to clear more timber at the base with a parting tool to help in seeing and making the outside line of his intended final shape. Colin drew attention to the fact that when you start to work at the top of a natural edge blank you are cutting through 'fresh air' at some points and that it is essential to watch the 'ghost line' to work out correct tool positioning. He worked on the outside shape and sanded it, whilst acknowledging that he would do further work on the outside lower half and would have to sand that again. He showed us an unusual but highly effective depth gauge that he would be using, and later he passed it round for inspection. To be brief the 'insert stem' could be described as a length of dowel split along its length and then glued back together but with an offset that would 'catch and hold' in a nick at the edge of the hole drilled in a flat strip of timber when simply rotated. So, you insert the shaft, move the flat strip down to the edge of the piece, rotate the shaft which will hold firm in the nick while you measure the depth of penetration. Phew! I hope that is clear. The bowl was hollowed with a gouge made very short by long use, and which he had had to modify to keep it in use. At the start it was necessary to lean right across the lathe bed to get the correct bevel rubbing position for the gouge. He gave the usual advice about removing any residual 'button' at the bottom of the bowl. Sanding with the water soaked abrasive needed great care and employed the wrist-gripping technique with the free hand. He reminded us of the need to always keep the abrasive moving when in contact to avoid unwanted scratches, and more work required to remove them. He said that slight surface dampness caused by his wet abrasive would soon dry off giving the option to finish with oil or wax. He mentioned that abrasives can be waxed if you wish. Parting off was achieved with exaggerated care to demonstrate the importance of ensuring that his sleeve could not catch on the rotating chuck. As with the vase the base was dished slightly in parting off to ensure stability of the standing piece.
Conclusion - I would guess that we all enjoyed that session immensely. We do not make personal remarks in reports such as this, but, I think it is fair comment to say that Colin's easy manner combined with fine attention to detail and a broad grasp of his subject made a very good impression on all of us.
<Top of Page>
The Show 'n' Tell Theme for the evening was An Apple and a Pear - not as well supported as some other themes - but, the quality was excellent, with some fine pieces on display.
![]() |
![]() |
![]() |
![]() |
![]() |
This entry from Richard Branscombe was commended as the 'most realistic pear!' |
![]() A Late Entry... |
![]() |
This month's winning entry from Harry Rock - the timber is believed to be Lilac and the stalks were made from Rosewood |
<Top of Page>