Club Night Report
Wednesday 14th May 2014
Club Night Report for 14th May 2014 - observations by Vernon HughesRoger Holley from Somerset took (most of) us into uncharted waters with his accomplished demonstration and talk on incorporating spun metal into woodturning.
![]() |
![]() |
![]() |
Before getting down to the practicalities, however, he took us into some of the history of bowl designs and use, particularly bowls used for drinking, and the introduction of metal into the designs, of which there are rare examples from Germany (Mazers) dating back a thousand years and usually only now found in museums. Some of these were lined and lipped with silver and even silver-gilt. A book 'The Wooden Bowl' by Robin Wood - was recommended as a source of information for anyone wishing to get into the subject more deeply. Timbers used included Maple burrs (more familiar to us as Bird's-Eye Maple), Ash, Beech, Alder, Box burrs (rare), etc. Many bowls (especially 10" diameter) had been recovered from the Mary Rose and were believed to have been drinking vessels due to the absence of knife marks.
Wassail bowls were also mentioned before arriving at the subject of quaichs (or quaighs or quoichs), the historic and famed two-handled Scottish drinking cups which had clearly captured Roger's imagination. Here is a sample quaich made by Roger but incorporating a woodturner's alternative to handles which would nevertheless achieve the key function of avoiding spillage of precious liquor. He went on to say that quaichs had a significant place in Scottish culture and were used in churches, on special and ceremonial civic occasions, as presentation pieces to individuals particularly in the armed forces and one had even been given as a loving cup by King James VI of Scotland to his bride before their marriage in 1600. They often incorporated metal on wood, the metals used including silver and pewter. This led into an examination of the composition of pewter (which historically had contained lead), and affirmation by Roger that the modern formula used in its manufacture relied on about 94% Tin combined with a small proportion of other safe metals - 1% Copper and 5% Antimony (lead is no longer used!). He would use it as the embellishing material in his demonstration.
Sources of supply quoted were the Wentworth Pewter Company (Sheffield) and its sister firm Quaich Co. (Scotland) Ltd.
He recommended, and would use in his demonstration, a 5" disc of very thin 22 gauge (about .64 mm or .025") marketed by Wentworth at 10 discs for approx. £25.
An alternative source of pewter discs can be found at: www.pewtersheet.co.uk - located in Birmingham. They offer any size of disc between 50 mm and 230 mm diameter in all thicknesses. They have quoted 125 mm diameter by .025" thick discs at £1.50 each (includes VAT) with no minimum order. Post and packing up to 1 kg is approx. £7.00.
Roger would show us how to apply a pewter lip to the rim of a bowl of diameter under 5". However, he passed round and had on display a pleasing range of metal-embellished items including an egg cup, coaster holders, a superb scoop, tea light holders, quaichs, bowls, etc.
![]() |
![]() |
![]() |
![]() |
![]() |
![]() |
![]() |
![]() |
This report will not provide an instruction sheet but will explain the principles and record some of Roger's sage observations. Two essential requirements for this work are an ability to make your own accurate jigs (formers) and associated components (from scrap or spare timber) and an original/ imaginative approach to creating suitable tools or at least their tips. Roger mentioned a tee shirt he had seen bearing the logo "He who dies with the most tools, wins". There is no need to be deterred by these demands though! Once understanding of purpose has been achieved it will be a matter of gaining familiarity through trial and error and practice. (Note: where you see two chucks in use together that was simply to overcome a mismatch between his drive spindle thread and our Club lathe.
The first jig used was designed with a shallow recess to hold firm a 5" disc from which the outer 1" or so would be removed to form the flange on the bowl. A neatly made wooden pad or back plate was used with tail centre support to stabilise the disc (and to give protection to its easily-marked surface), and masking tape was used to keep the carefully measured cut-off section in position after the parting cut was made. This can be done with a skew or other suitable tool (Roger had modified a scraper and had given it a V-point). The result was a large washer!
The next jig or former (colour coded to permit quick identification amongst a kit of many for the different sizes of the range of items he makes) was used for turning over the outside, then inside, edges of the pewter ring to form a flange for fitting on the bowl rim. A back plate was used to hold the flat metal in position while the outside edge was turned over using his own design of special tool.
Tools used in metal spinning should generally be 'sturdy' to accommodate the pressures involved - and be highly polished on the 'working end' to assist the flow of the metal and to avoid marking it. Use a low spindle speed - 450 rpm was about right. Also, use a 'lubricant' when spinning the metal - Roger used a wax polish for this.
With the partially completed flange ready - he then prepared the rim of the (receiving) bowl with close attention to precision. Contact adhesive was then applied and the flange was positioned on the rim (again very precisely) and a pressure disc was used to press the flange fully home on the bowl rim. Fine (small) undercuts had been made on the outside and inside of the bowl rim to receive the edges of the flange when they were turned over firmly to slot into them.
Roger concluded by saying that the pewter can be polished with any non-gritty polishing substance (e.g. 0000 wire wool and Solvol Autosol - metal polish, were mentioned) and could also be varnished if so desired. The residual small central disc would be used when decorating some smaller item.
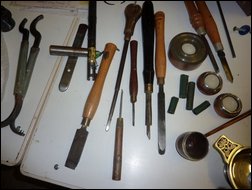
Sources for designs and proportions included Richard Raffan, Ray Key, ceramics and artistic glassware, etc.; manage the swarf produced when working metal very carefully, to ensure that it does not reach bearings (especially at the headstock); design of the wooden articles turned to receive metal should be kept fairly simple because it is the contrast between the two materials that gives the finished items their appeal; pewter marks easily so protect it as far as possible but light scratches can be worked out readily enough; make specially shaped small tools to reach inaccessible places, e.g. use Allen Keys which are very hard; adapt whatever you like to make the tool shapes needed and apply the same thinking to jig designs; timbers used should be dry but pewter will flex to absorb small movements of the wood.
Notes: The word quaich can be traced back through Scottish Gaelic, Old Irish, Latin (for drinking cup) and Greek.
An idle thought - Is there any scope for us to use metal decorated quaichs, etc. as presentation items?
<Top of Page>
The Shown 'n' Tell theme for the evening was A Goblet - this was well supported with varied and interesting items on display.
![]() |
|||
![]() |
![]() |
![]() |
![]() |
This month's winning entry is a natural edged goblet made in 'wet' Ash by Bob Wells. It measures approx. 6" diameter by 7" tall and has a wall thickness of around 3 mm. |
![]() |
<Top of Page>