Club Night Report
Wednesday 13th March 2013An evening with Melvyn Firmager - observations by Vernon Hughes
This was not a night for the faint-hearted. Melvyn (Website: www.nuttreefarm.com/SchoolOfWoodturing.html) had laid out a large range of his mostly mammoth (say 4ft long) own-design tools, and it felt like walking into an old armoury to choose a new sword from a gleaming heap. Size matters if you are a hollow form/ sculptural turner such as Melvyn who revealed that these seeming monsters were counted as only medium length by some specialised turning experts. Jaws dropped further when he said that on his own familiar equipment his tools could remove an inch of timber per pass and that he was used to roughing out basic shapes in next to no time. However, limitations in our lathe's performance (surprisingly underpowered for Melvyn's purposes) meant that his cuts were thinner, and on several occasions tools jammed solid and brought the lathe to a halt. One gouge was of more conventional length though and was highly favoured because he had applied an 'Irish grind' which gave exceptional and smooth cutting efficiency (more anon), and he used a couple of small but uniquely ground 1/8th inch parting tools more familiar to ordinary mortals. He also said that he had turned to his advantage the tendency for gouges to become pointed when ground without use of a jig. Taking the points to a more extravagant level had led to his des
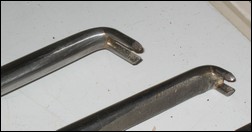
All his tools were highly specialised in design including many with cutting tips welded on short bars at right angles to the main shaft; and there were specially designed dual tips. For the purposes of this report though it will be best to acknowledge that they are as highly specialised as they are efficient in use and leave it at that. An appreciation of the designs is not possible in a short article based on one (first) viewing of the tools and their potential.
Lack of a rotating headstock prevented demonstration of the advertised sculptured hollow forms but he adapted readily to show his way of producing a narrow-necked vase with a
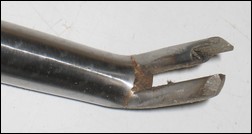
To round off this report I will pick out from my notes some points of particular interest, or tips he gave throughout the proceedings, starting with the immaculate 'Irish grind'. I took a close look at the gouge as he was packing up and he explained the principles of its shape and how to achieve it on our own grinders at home. The bevel can be at whatever angle you prefer but the crucial point is that the long tip edges must be at a width narrower than the cross section diameter of the bar. Do we have members who are competent at this highly valuable form of tool preparation I wonder? It would be very helpful to practice this shaping under the guidance of members who knows exactly the whys, wherefores and hows?
Other Points: It is a very sound idea to make collars for our toolrest posts so that each rest will settle automatically at an optimum height and thus save time in fiddling to get it just right.. Melvyn uses a single size but added that Basque turners have different collars to suit every type of tool. (Note: for example - we all know that rest height must be raised when using scrapers). He emphasised the importance of lathe height, stance, posture, minimal foot movement and tool handle held firmly against the hip to make tool management easy and to obviate fatigue. With long tools an overhang of say 10 inches could be managed easily with the correct tool-to-hip/ swivel discipline. He used an unusual faceplate having six screw holes all angled inwards to give added strength of grip. His tools (some?) incorporate cobalt/ steel tips which tolerate much higher temperatures than the usual HS steel. He supplies capilliary tubing suitable for controlled application of low viscosity superglue, 'woodturner's scotchbrite', tools etc., and he has a catalogue - (there must be a website but I have not found time to check). When working with wet wood keep a bucket of water handy to dip gouges in. This will clean up the flutes and reduce frequency of sharpening. For his second demo item he mounted a square blank and took the corners of using one of his mighty tools!
During the evening he took an interest in all Club-turned items presented for his inspection and gave sympathetic but honest critiques of both design and workmanship.
Conclusions: If we can all learn to apply an 'Irish grind' to at least one gouge we shall have taken a first small step on a long trail blazed by an international master.
Vernon Hughes
17th March 2013
![]() |
![]() |
|
![]() |
![]() |
<Top of Page>
March Meeting - Project 100 turned by Vernon Hughes
This month's Project 100 featured a 9"square by 3" thick block of Oak. This is over 200 cubic inches - but serves to illustrate the informality of the Project 100 'rules'.
On initial inspection Vernon found that the blank had some obvious flaws - some soft sapwood that had been attacked by bark beetles and some shakes in the end grain. During his description of how he made the part Vernon drew attention to these 'faults' - mainly to alert newer turners to the importance of examining a piece of wood before mounting it on the lathe in order to make the most of it, and to address any visible flaws in deciding on the design - in this case a rimmed bowl.
The blank was mounted so that the sapwood and beetle damaged areas would be turned away in shaping the underside of the bowl. In the event only a little timber was lost in cleaning the surfaces at top and bottom of the bowl. So, after all the shaping the bowl can still be described accurately as a nominal 9" diameter x 3" tall.
Vernon also made a small 'joke' light pull from one of the scrap corners of the blank!
![]() |
![]() |
<Top of Page>
The Show 'n' Tell Theme for the evening was "A Hollow Form" - here is a selection of the items displayed:
![]() |
![]() |
![]() |
||
![]() |
![]() |
![]() |
||
Winning Entry for March 2013 This hollow form was made from Spalted Beech - and stands 7" tall by 3.5" diameter |
<Top of Page>