Club Night Report
Wednesday 9th July 2014
Club Night Report for 9th July 2014 - observations by Vernon HughesJust for the record our demonstrator for the evening - Paul Hannaby turned out to be from The Forest of Dean (Gloucestershire), not the West Midlands as shown in the programme; and he gave us more than advertised by demonstrating an approach to colouring turned work before the break as well as the expected natural edge work afterwards. When the first bowl decided to leave the lathe prematurely Paul gave an object lesson in imperturbability and showed a mastery of the recovery process in a situation where many a turner would have given up. Paul produced two bowls, one on each side of the break, and demonstrated an ability to perfect the insides solely with sweeping cuts to a standard of perfection rarely seen. There was no recourse to scrapers for interior finishing; the gouge achieved perfection.
A visit to Paul's website at www.creative-woodturning.com is an eye-opening 'must'!
![]() |
![]() |
The first bowl was started using a screw-chuck-mounted octagonal-shaped, dry oak blank of dimensions approx. 7" across and 4" thick. Why spend time producing circular blanks he asked? He faced off the blank using dragging cuts to ensure that they always moved 'downhill' - i.e. avoiding lifting end grain. This included formation of the (very short) dovetail spigot. Unusually, he shaped the outside form using a spindle gouge and concentrated throughout on cutting sidegrain, first in one direction only before moving to both directions. He took care to mark the centre point of the spigot, a strongly recommended action for all turners to provide a reference point for later use if a mishap occurs - and also for centralising when re-mounting to complete the base. He also emphasised the importance of making spigots to the exact size to match the chuckmaker's (jaw) design intentions so that the spigot is gripped around the full circumference surface to achieve maximum holding. He also focussed on the point that there is no need for a long spigot that reaches to the internal base of the chuck jaws; but the interface between jaws surface and bowl base must be perfect as that eliminates space for movement. After completing the external shape of the bowl he perfected it with exceptionally fine shaving cuts and then bent a long gluestick over the shape to demonstrate how to check for any high and low spots in the turning (none in his work of course!). Using a thin flexible steel rule was another option.
![]() |
![]() |
![]() |
![]() |
![]() |
![]() |
Paul then moved to the external decoration options which started with acrylic white gesso primer (sourced from an art shop). That requires a two hour drying period so he switched to a bowl 'made earlier' to demonstrate an approach to colouring employing two types of air brush - single and double action versions. Using a small electric air compressor to power the air brush - various airbrush acrylic paint colours were applied - magenta, then manganese plus some purple and finally a faint hint of black, all carefully merged to make a distinctly artistic and colourful effect. Seal with several coats of acrylic satin spray lacquer. Note: if it all goes 'wrong' or you do not like the effect you have created - then just sand it all off and start again!
The bowl was then reversed for internal shaping (with the spigot mounted in a chuck).
With bowl gouge braced firmly to his side Paul applied hard swinging cuts straight away which resulted unexpectedly in sufficient damage to the spigot to cause it to escape the chuck's grip. Paul's analysis was that the initial cuts were unduly strong for the very dry (brittle) character of the timber which had been unable to take the strain. However, this did not undermine the earlier advice about how to approach spigot shaping and precision. In this case it was the spigot that failed, not the chuck's grip. Space and time do not permit a full description of Paul's very impressive recovery procedure. Suffice to say that he re-reversed the bowl accurately using a cup centre in the tailstock and a 4-prong drive centre, and re-cut the spigot before once more tackling the hollowing process. With his wide-sweeping-curve action he soon repeated the external shape on the inside of the bowl and aimed for a 5 to 6 mm wall thickness. He touched briefly on the wide range of choice for edge shapes and advised us to take account of the change which occurs in cutting speed as the tool moves from the fast-rotating outside edge to the centre point where the timber is almost stationary. He then focussed hard on tool action at the bottom of the bowl where, provided a short bevel gouge is used, and the bottom of the bowl is perceived as almost 'flat', it is possible to achieve a perfect bottom line from the gouge without recourse to scraper use (very impressive). Finally he cautioned us to respond quickly if a 'ringing' sound is detected in the late stages of hollowing. Firstly, back off to check everything and then remember to apply downward pressure and take pains to avoid pushing outwards!
![]() |
![]() |
![]() |
![]() |
![]() |
![]() |
![]() |
![]() |
NB: After a supremely well-deserved round of applause for Paul's impressive demonstration, I examined the inside of the bowl, particularly the base. There was not the faintest trace of a residual pip. That level of perfection from the bowl gouge must surely take some learning and skill development! This had been yet another fascinating demonstration delivered by a very safe pair of hands.
<Top of Page>
The Show 'n' Tell theme for the evening was A Finial Box - this was well supported with varied and interesting items on display.
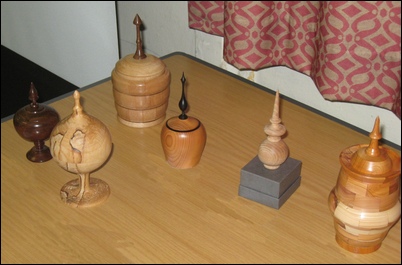
![]() |
![]() |
![]() |
Arthur Kingdon announced the results in 'reverse order' to say that Roger Blake with a Silver Birch globe box (shown on the left) along with
Fred Lumsden with his segmented Yew box (shown in the centre) had been placed joint third.
Harry Rock was this month's Show and Tell winner with a tapered triangular shaped Ash box, with a Padauk loose fitting lid and a Holly finial. Height of the box including the finial is 7 1/2".
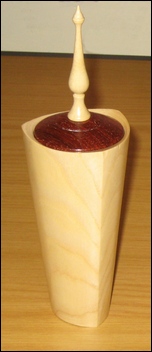
The Display Table showed some ornamental style turning in alternative Ivory, a natural edge vase and two 'Green Man' pyrography boards.
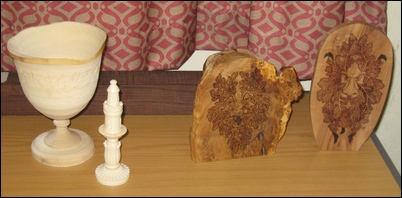
<Top of Page>