Club Night Report
Wednesday 10th July 2013An evening with Gary Rance - observations by Vernon Hughes

Gary introduced himself by explaining that he is (yet another) product of the old apprenticeship system in which repetitive turning (of domestic items in his case) was the order of the day. When he started his apprenticeship (in Buckinghamshire) all the machinery on the premises was belt driven from a steam engine, and variable speed lay in a 'yet-to-be' electrified future. The full story of his career can be read on his comprehensive website (www.garyrance.co.uk/about-gary); so it is only necessary to record here his mention that he has never been a 'hobby' turner - but turning is how he makes his living, without the need to diversify. He then proceeded to give us a 'what it said on the tin' and a good deal more.
He dealt with the Use of The Round Skew, Pendant Making, Small Ornamented Box Making and a brief demonstration of his method of tool sharpening.
Round Skew - During the 'skew' phase Gary demonstrated its use in making the conventional shapes we all produce in spindle turning generally and the resulting work was circulated for close inspection. The tool was formed simply from a half-inch diameter HSS bar, ground to be 2 degrees 'off-square'. This resulted in the tool being not as 'pointy' as
the usual skew angle. Advantages of
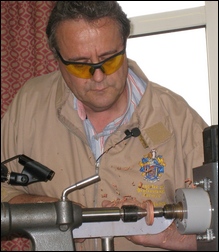
Pendants (with offset hole) - I have a closely written page of notes on his demo but the best way to learn all about his method and technique is to obtain a copy of his DVD on the subject (see Gary's website - cost £17). The technique rests firmly on a special offset jig he has designed for use in a 4-jaw chuck. As with everything he makes, Gary achieves a very fine finish but he said that ultimately, it is the smart cardboard box that clinches sales!
Small Box - He made expertly one of his superb small boxes.
The wood employed was Mexican Rosewood (aka Bocote) and
the lid was inlaid (Gary's technique as closer to an '
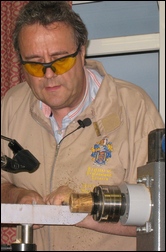
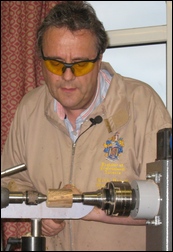
In brief he used the classic technique of making a spigot at each end of his cylindrical blank and then parted off the lid section, mounted it in the 4-jaw chuck using its spigot and turned and finished the inside. The body was then re-mounted on its spigot and its top shaped to receive the lid with a tight fit. He then went on through the usual steps but produced one move that I have never encountered heretofore. At a late stage, with the lid jammed on tight, he placed the end of a bar of soft wood (in cold chisel mode) against the finished lid edge and hit it hard with a hammer to remove the lid. No mark was left on the polished surface/ rim, but he emphasised
that the bar must be 'soft'. He was
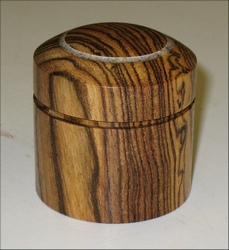
The finished box was a beauty notwithstanding the finesse needed to apply the Corian detail, a typical product of turners of his calibre.
Tool Grinding - Gary emphasised that the grinder must be mounted so that it is chest high in use; avoid a bending over the wheel stance! He showed his method with a number of tools but I found the spindle gouge the most interesting, carried out without the use of a jig. He concentrated solely on the rounded tip first and only when satisfied with that did he apply the usual long upward strokes to the wings. Most top turners can combine these two actions to achieve the desired 'lady's fingernail' form, whereas many amateurs end up with a point when attempting that method. For myself, I take the easy way out with a Robert Sorby fingernail jig. You have to position the gouge accurately in the jig, but once that has been achieved it's a 'piece of cake'!
Conclusion: How do these top chaps cram so much into such a short time and with such quality? You have to wonder how turning will look in the not too distant future when the supply of tool-savvy turners grounded in repetitive workshop production (such as Gary) dries up.
<Top of Page>
The Show 'n' Tell Theme for the evening was "A Matching Pair" - although this was somewhat poorly supported the quality was excellent!
![]() |
A Chess Set in Rosewood
and Holly
|
![]() |
![]() |
This months winning entry from
Allen Cook - timber is Bubinga |
![]() |
<Top of Page>