Club Night Report
Wednesday 15th January 2014
Club Night Report for 15th January 2014 - observations by Vernon HughesThis was another occasion for reliance on our own in-house resources.
This time one member was to keep us occupied for the whole evening, and it turned out to be the valiant Richard Branscombe. He said that he had responded innocently to the call for volunteers when a trawl for 'likely lads' was made several years ago, but with the passage of time that had slipped from memory so it had come as a shock when his name suddenly emerged from the hat. He did not mention it but we should keep in mind too that he had used up quite a lot of ammunition in June last year when, it will be remembered, he shared presenter responsibilities 50/50 with our Chairman. So what shots were left in the locker?
![]() |
![]() |
![]() |
![]() |
Care was taken over the top edges of the vase, including retention till the last minute of the final slice of MDF, to ensure a neat/ unblemished finish. Richard offered two further pieces of advice in the margins, viz: it is advisable to give the inside of the vase a couple of coats of polyurethane to waterproof it and secondly when considering vase designs and shapes it is a good idea to seek inspiration from equivalents in glass and ceramics. In rounding off this part of his demo Richard created a thin, flat jam chuck (just like that) for stabilising the vase top in the finishing process and dealt with the final external shaping, etc. To save time he did not sand, polish or decorate the vase but displayed numerous examples of appealing, finely finished and/ or decorated pieces.
![]() |
![]() |
![]() |
![]() |
After the break Richard made three more pieces: a small twig pot in Elm, a rapidly-made, truly miniature vase from a conifer twig followed by an off-centre vase.
His purpose in the last-mentioned was to demonstrate the method more than to achieve a finely finished piece, but two examples (of items made earlier) were on display. The 8" long by 3" diameter blank had been partially shaped off-lathe beforehand with a 'lump' projecting to one side at the base. Richard explained that he worked roughly to a proportion of stem to base of 2/1 which is fairly close to the golden mean. It will be seen from the photographs that the two centre-lines run parallel in this mode of off-centre turning (i.e. no angling is involved), the base being off-centre from the main stem centre. It is necessary to decide in advance the measurement to be used between the centres and to mark these out accurately at both ends. In this form of turning it is essential to get used to watching shadow lines throughout.
The order of work involves completing the stem in all respects before tackling the base. The blank
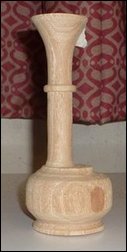
A concluding observation about Richard's approach is that no work-mounting or tooling challenge will ever be too much for him! He will devise any and every accessory needed to hold securely, and work, any piece of wood, and he makes it look so 'quick and easy'. As he explained last year he started work in 1951 as a dockyard apprentice at Portsmouth and it is clear that in those days they taught skills, methods and self-assurance to last a lifetime. I'm not surprised. I joined the Admiralty seven years later and became familiar with dockyard and shipyard activity.
<Top of Page>
The Show 'n' Tell theme for the evening was: Open Theme - just bring along an item you are particularly pleased with - this was well supported and a number of excellent turnings were on display:
![]() |
![]() |
![]() |
![]() |
![]() |
This month's winning entry was a lovely bowl with inserts, and a carved and coloured design by Brian Oram (on the left) discussing his entry with Mike Crawshaw (Chairman) |
<Top of Page>