Club Night Report
Wednesday 9th January 2013For this meeting we were entertained by two of our own Club Members - Brian Oram and Arthur Kingdon
The first presentation and demonstration was from Brian Oram - Club Member and published author - Turning Pigs
If you want to know how to make beautiful and fun turned animals then Brian's your man. After 35 years of woodturning Brian Oram brought an entirely novel idea to our January meeting explaining in detail the stages involved in making a "family" of turned pigs. It was fascinating to follow the process from start to finish and see each whole animal take on both form and character. He passed round design drawings, partly made components of each pig, and tools, for example a very useful home-made "star sander" for sanding into crevices. This made the whole process really come to life for the audience.
The basic stages for each pig are:
- Choose the appropriate size square cross section wood block for the pig
- Drill the 4 leg holes square to the block side
- Turn the block down for the body; sand
- Turn 4 legs and fit. Brian uses a bead cutting tool for shaping.
- Turn the 2 ears, hollow out shape with a very small carving gouge and fit
- Face - cover the top of the face with masking tape, drill eye holes and fill with a mixture of Polyfilla, PVA glue and black water colour paint
- Chisel out mouth
- Drill out nostrils
- Sand all 4 feet simultaneously on a sanding disk to make sure the pig stands perfectly
- Tail - make either from copper wire wound round a nail (a bit sharp for children?) or from nylon cord soaked in PVA
- Finish with 3 coats acrylic clear varnish, sanding to 400 grit between coats
Brian has published the book: "Turn an Elephant and Twelve Other Projects to Hone Your Woodturning Skills" offering less experienced woodturners an easy to follow, step by step guide with photos to turn 12 different projects. The book is available in the club library or you can buy your own copy from:
www.authorhouse.co.uk/Bookstore/BookDetail.aspx?BookId=SKU-000459824
Chris Frankum
12th January 2013
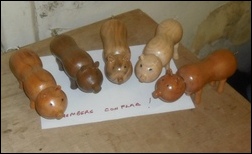
<Top of Page>
The second presentation and demonstration was from Arthur Kingdon - Club Member, talented underwater photographer and Ornamental Turner - Rose Engine Turning
Arthur Kingdon introduced the audience to the art of Ornamental Turning (OT) which has been his passion for many years. He started with an historical overview of the subject showing several images of medieval turning achieved using a Rose Engine (RE) and the Victorian style of turning done on an OT lathe. He showed the difference between 'plain' turning and OT where the item is first plain turned to size before being held stationary, whilst being drilled or having material removed by rotating cutters. He passed around examples of his work, as well as passing around a variety of cutting frames both antique and modern.
Arthur showed images of several very fine antique lathes but was keen to stress that excellent work can be done on much more modest equipment. He showed images from some of the leading turners in the UK, followed up by images of the equipment they used - some of it very basic indeed!
Rose Engine work is achieved on a machine that has a headstock that can rock, pivot or slide, or a sliderest that can copy these movements - some very fine work is now done on user-made CNC machines. Some machines can produce a much different style than that achieved by using rotating cutters, provided the machine is robust enough to allow fixed cutters to be used. The medieval style of convex forms can then be achieved. Rose Engine lathes can be extremely expensive and complicated but Arthur showed a simple but ingenious RE that can be built using half a sheet of MDF plus a few metal parts. This created a lot of interest while he demonstrated how an attractive pattern can be cut relatively easily and quickly.
Useful Links:
The Society of Ornamental Turners www.the-sot.com
John Edwards (Information, items for sale) www.ornamentalturning.co.uk
Paul Coker (Professional Turner) www.cpaulcoker.co.uk
Steve Ellis (Rose Engine information) www.roseengine.co.uk
MDF Rose Engine Plans (Note: 2.2 Mb PDF file download):
www.woodturner.org/products/aw/howto/rose/MDFConstruction_v6[1].pdf
Arthur Kingdon
12th January 2013
Rose Engine Details:
![]() |
![]() |
![]() |
||
![]() |
![]() |
![]() |
<Top of Page>
The Show 'n' Tell Theme for the evening was "Any Turned Item" - here is a selection of the items displayed:
![]() |
![]() |
![]() |
||
![]() |
![]() |
![]() |
||
![]() |
![]() |
![]() |
||
Thanks to Ron Headon for all of the photographs on this page |