Club Night Report
Wednesday 13th August 2014
Club Night Report for 13th August 2014 - observations by Harry RockThe demonstrator for the evening was our own, home-grown talent - Club Member Ron Headon - whose chosen subject was "Turning Wooden Jewellery". Ron's preamble stated that he was going to show a mix of a PowerPoint slideshow using the projector and live demonstration on the lathe. He was going to show as many of the tips, tricks, techniques and tools that he used to make wooden jewellery - basically, it's all about small scale woodturning! Making jewellery is also an excellent way of using up scraps of exotic and unusual timbers. A first-rate book on the subject is: "Woodturning Jewellery" by Hilary Bowen (currently on Amazon at £13.72)
![]() |
![]() |
![]() |
Ron started with the PowerPoint to show the list of subjects he intended to cover for the evening:
* Drop Earrings and Beads
* Stud Earrings and Brooches
* Hooped Earrings
* Pendants
* Laminating
* Bracelets
* Alternative Materials
He light-heartedly summed up the different kinds of jewellery as: "stuff you stick into yourself" (earrings - drop, beads and hoops), "stuff you hang off yourself" (pendants, bangles, bracelets) and "stuff you stick onto clothing" (brooches, cuff links). He would not be completing any of the items with the application of a 'finding'. These are the metal components that attach to the woodturning to facilitate the wearing of it. It's a huge subject with its own specific terminology to include: studs, posts, clasps, scrolls, jump rings, bolt rings, pegs, thongs and hook wires! See this website for illustrations, purchase etc. www.cooksongold.com
The demonstration began with the creation of a drop earring, using a lace bobbin drive (a Morse taper shank with a square socket to drive the wood) in the lathe headstock and supported by the tailstock centre. The timber selected was Padauk. The blank was roughed to a cylinder and a 10 mm spigot turned on the tailstock end. This was then transferred to the Axminster Junior Chuck - a small collet chuck that is particularly suited to jewellery making - see: www.axminster.co.uk/axminster-junior-chuck (current price: £42).
He then held a small pin chuck in a Jacobs chuck, in the tailstock to drill a 0.5 mm (.020") diameter hole for the finding. An alternative might be to hold the drill in a pair of pliers and to 'freehand' drill the hole. Both methods carry a high probability of breaking the drill bit! The shape of the earring was then turned, sanded, finished and parted off. During the finishing stages, colour could be applied to create interesting effects. Beads would be made with the same technique (round, diamond, dished, oval shapes etc. - in different sizes). Clearly, you would often need to make the items the same - i.e. as part of a pair - so Ron demonstrated that the use of a gauge/ scratch stock to mark out the timber would be useful.
![]() |
![]() |
![]() |
![]() |
Stud earrings are ball shaped (holes not required) - with a small flat and are superglued to a finding called a post - and held in the ear with a 'scroll' on the post.
The next item to be turned was a Hoop Earring - made from square stock - roughed to a cylinder between centres. Once again the tailstock end was turned to a 10 mm diameter spigot and then re-mounted in the Axminster Junior Chuck. Ron then proceeded to true up the outside diameter, and used a part off tool to set the width of the hoop. A small bowl gouge was then used to bore through and shape the front face of the earring. Sand and finish this front part of the earring - then part off, remount and complete the other side.
After the break, Ron returned to discuss and demonstrate the making of Doughnut and Hoop earrings. Doughnut earrings usually have a concentric hole - and Hoops often have the hole off-centre. He showed an excellent selection of inspirational examples via the projector. A Pendant design is very similar - and is mounted on a neck chain or often a leather thong. The use of wooden faceplates (attached to a metal faceplate or held on a dovetail spigot in a chuck) and hot-melt glue were good ways of holding the item for turning. For turning the other side of the hoop/ pendant - the item could be held in a jam chuck or alternatively a 'split collet' could be made. This would then be held in a chuck to compress the collet to hold the work. Another alternative would be the use of custom/ home-made jaw plates - which can be machined to hold any size or shape.
![]() |
![]() |
![]() |
![]() |
Wood, of course, is not the only material that can be used for jewellery - Ron discussed the merits of the usual pen-turning materials (just the right size for earrings) to include acrylics, dymondwood, and Tagua nuts (alternative ivory).
Conclusion: Ron did a splendid job with a challenging and wide ranging subject! Well researched, well prepared, and expertly presented with liberal doses of humour on the side. Thanks Ron!
<Top of Page>
The Show and Tell theme for the evening was A Natural Edged Item - this was well supported with varied and interesting items on display.
![]() |
![]() |
![]() |
![]() |
![]() |
![]() |
Ian Full announced the results in 'reverse order':
![]() |
![]() |
Arthur Kingdon with an Acacia bowl that he was not particularly pleased with, there is a lot of super glue holding the bark on - although he thought the final result was OK (ish). Arthur said this bowl had reminded him that we should turn an item for the beauty of the wood, not the maximum size we could produce from the blank.
Bob Sawyer with a Yew winged bowl - "a bowl for a banana" - finished in sanding sealer and wax.
![]() |
![]() |
Harry Rock was this month's Show and Tell winner with a Laburnum off-centre vase - approx. 8" high - finished in Danish oil and wax. It was turned 'wet' and proceeded to split at the rim as it dried out. The work was 'saved' with the addition of some decorative copper wire 'stitching'…
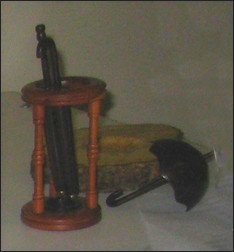
<Top of Page>